
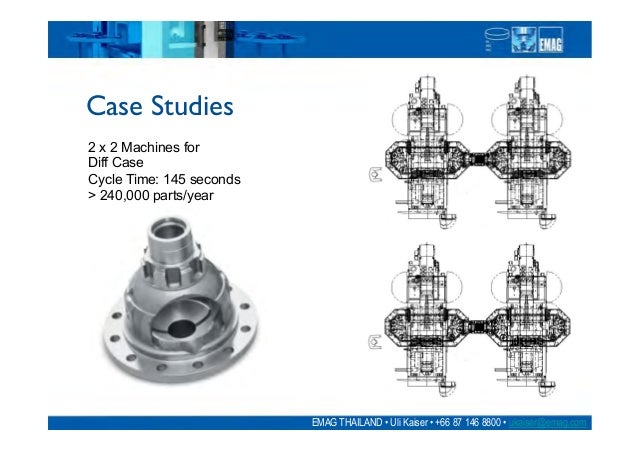
Hogge says this system enabled the shop to run the job without an operator.
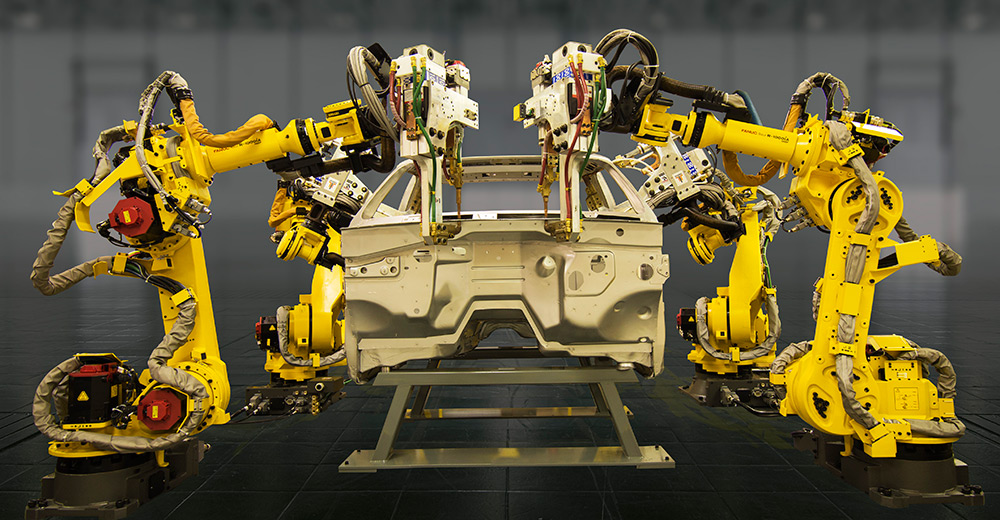
The company markets this invention as the “Rota-Rack,” and Hogge Precision Parts learned about the product from machine tool supplier Machinery Solutions. To solve the problem, the company invented a carousel system for gently removing and collecting finished pieces. The maker of machine tool accessories in Hauppauge, New York had been damaging lathe centers by allowing them to drop from the CNC lathes producing them. As long as labor was significant to the process, the expense of that labor would make machining in China a lower-cost option.Īs it happened, Royal Products had faced a similar problem. “We had an employee standing at the machine unloading it by hand, but we couldn’t keep the job that way,” Mr. As a result, a part could complete the machining cycle successfully and be ready to ship to the customer, only to be scrapped because of what happened when it left the machine. When a finished piece dropped from the turning center’s exit chute into a bin, it would often damage another piece it landed on. The part was heavy, valuable and made from a soft metal, Mr. The automation in question was not for loading the work, but for safely removing it from the machine. Sidebar: Workhandling Keeps Work in The United Statesįor Hogge Precision Parts, workhandling automation proved key to saving a job that came close to being sent to China. Gone, now, is the expectation that human eyes or human hands will be involved with any job as it runs. But at the same time, the mindset this staff brings to production had to shift to embrace going lights-out. Their mechanical experience came fully into play, because the imperfections that had to be addressed to bring the CNC machines into unattended production generally were mechanical problems. Various senior employees date from when the company was a screw machine shop. In fact, the commitment of these employees was vital. The creativity of Hogge Precision Parts’ employees was among the enabling factors that made the move to unattended production possible. Certain other changes are proprietary, because staff members overcame some glitches in imaginative ways that they hope competing shops won’t figure out soon. It also implemented quick-change Capto tooling from Sandvik Coromant at tool turret positions subject to frequent change to speed setup of new jobs at the end of the day shift. These are just a few areas in which the shop adapted its technology and thinking for unattended production. It knows which machines are stable enough to run the finest-tolerance jobs through the night. As a result of studying this problem, he says the shop now knows more about the thermal temperament of its machine tools than ever before. Knowing which machines hold their positioning is valuable for running lights-out, because temperatures change considerably during the course of an unattended shift. His most thermally stable machines have proven to be some of the older ones in the shop. Hogge says the answer might surprise you. What level of thermal stability does any given machine provide? Mr.
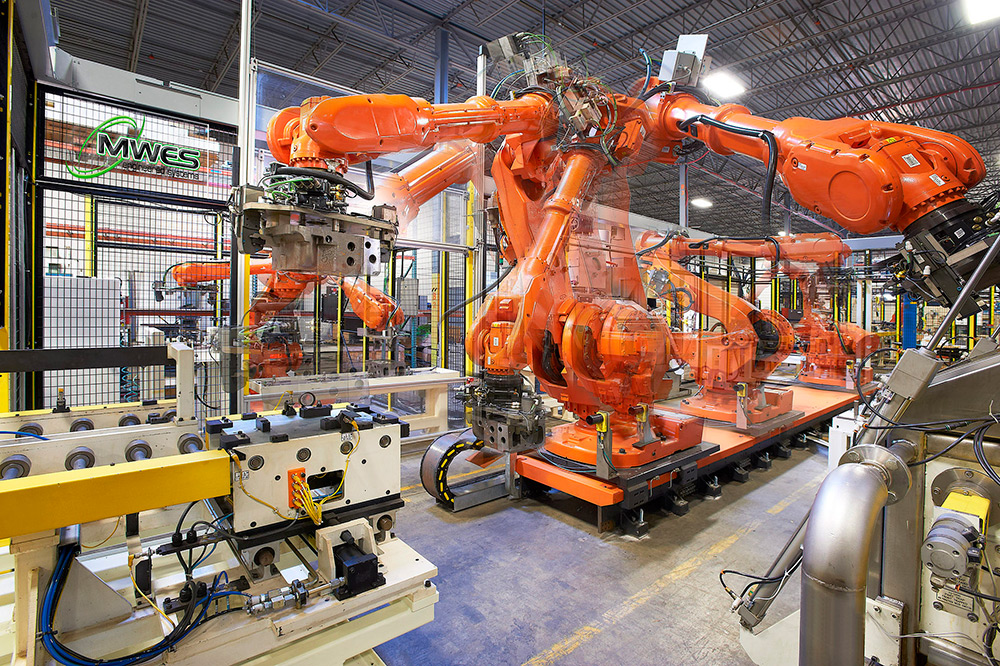
A workhandling device that prevents this, a device the shop embraced as part of its journey into unattended machining, is the Rota-Rack unloading carousel from Royal Products (see sidebar).Ĥ. When large production quantities run without an operator to retrieve parts by hand, workpieces falling onto workpieces can cause damage. Part unloading is at least as important as how the part goes into the machine.

While such problems are uncommon, knowledgeable operators spot them and address them easily enough that shops might underestimate how frequently they occur.ģ. Something similar might be true of a chip wedging into a strange spot to affect the subspindle chuck, or a cutting tool breaking instead of gradually wearing. By day, the problem went unseen, because an operator noticing that the lathe was not cycling could clear the error and resume production within a minute or two. A bar feeder loading material into a lathe might fail to trip a switch properly only on rare occasions. Any process on any CNC machine might be susceptible to eight to 10 infrequent production-stopping problems, all of which had to be discovered and resolved before the process could be trusted to run with no employee present.Īgain, these were not big problems. Hogge says, because successfully resolving a problem that halted production one night could simply reveal another problem that would halt the same process on a later night. The way through this journey was often infuriating, Mr. That is, it was a journey of fixing previously tiny problems that became large, and previously invisible problems that became visible, once the machines started to run with no operators present.
